Table of Contents
Summary:
A product designer has used SHINING 3D’s EinScan-Pro 3D scanner to scan an European-style carved board and an eight-note music box movement as part of the reverse-engineering and design of a new product. Then, he used of SHINING 3D’s industrial-3D printer iSLA-650 3D printer to produce the final artistic music box.
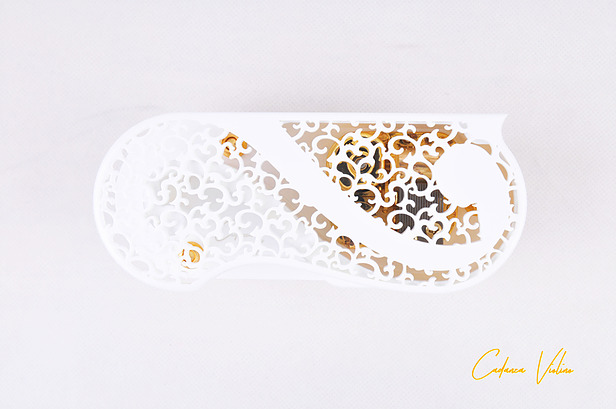
Customer Profile:
“The Cadanza Working Studio” seeks to integrate the elegance and beauty of classical music into its product designs. At the same time, Cadanza also uses the latest technologies, such as 3D printing, in the manufacturing process to create distinctive and automized products for consumers.
About the Case:
Sheldon, designer of the “Cadanza Working Studio”, is an aficionado of classical music. He is also a great fan of classical Western musical instruments, such as the piano and the violin, as well as the decorations on such instruments (such as the elegant and beautiful European-style carved surfaces). At the beginning of his new music box project, he decided to make use of the 3D scanner to integrate the European-style carving pattern into his design.
1. Early stylistic design
The designer created a sketch that showed the approximate appearance and style of the music box. The approximate outline of the product was also created in the design software.
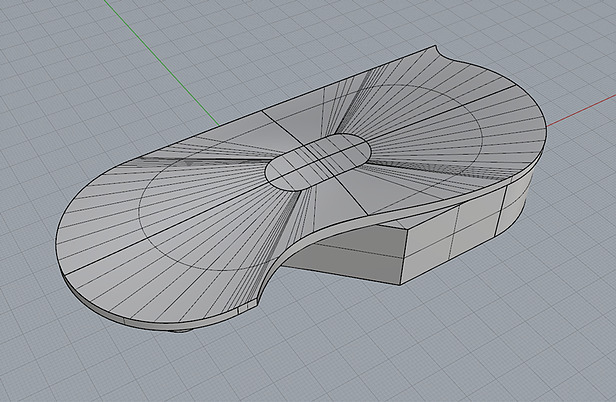
2. Conceptualizing the scaning plan
After the early stylistic design was complete, the designer determined the parts that would require the use of the 3D scanner. The designer decided to make use of the 3D scanner to aid the design of the product in two ways.
First, the 3D scanner was used to scan the European-style carved board to obtain scanned data of the carving pattern which would then be integrated into the final design of the music box.
Second, the 3D scanner was used to scan the music box movement to aid the structural design of the music box movement.
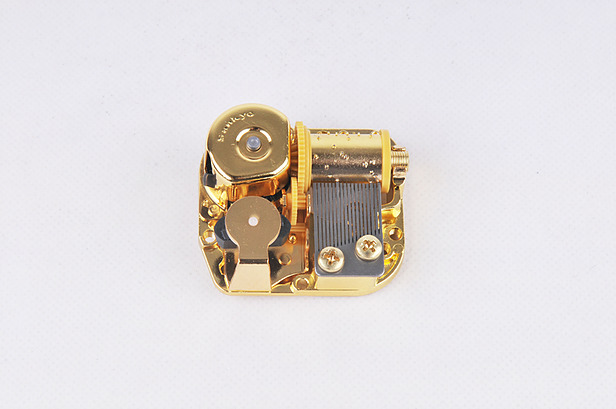
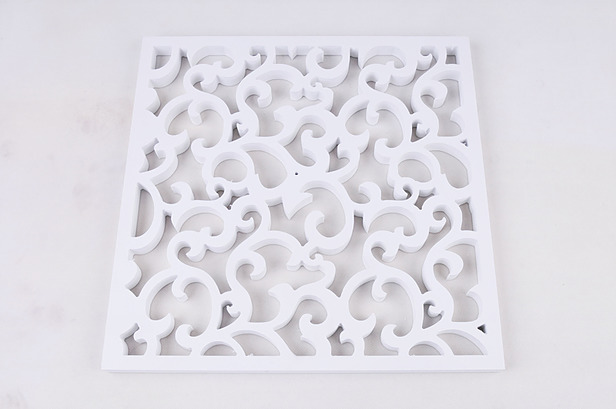
3. Scan the model data
Scan of the European-style carved board:
The designer used SHINING 3D’s EinScan-Pro 3D handheld scanner to scan the European-style carved board. The designer switched the build-in software of the scanner to the handheld HD scanning mode to perform the scanning with the designer held the scanner in one hand and the carved board in another hand. As the scanning going on, the scanned data were shown in real time in the software interface on the computer screen. The 3D scan of the board was completed in around ten minutes.
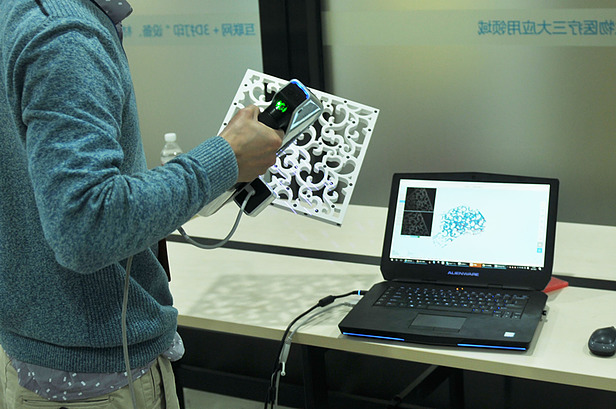
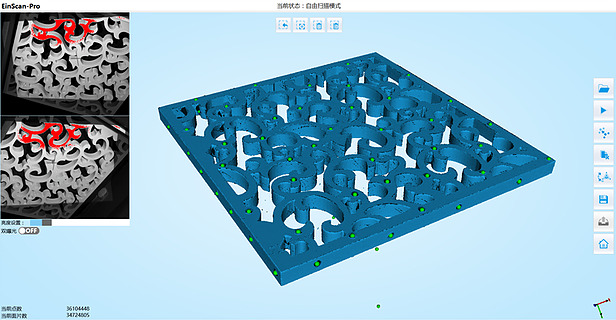
Scan of the music box movement:
After the scan of the carved board was completed, the designer moved on to the scanning of the music box movement. The designer placed the EinScan-Pro on a dedicated tripod and the music box movement on a turntable. Then, he switched the scanner to automatic scan mode. Scanned data of the music box movement was quickly obtained with the pairing of the turntable and tripod.
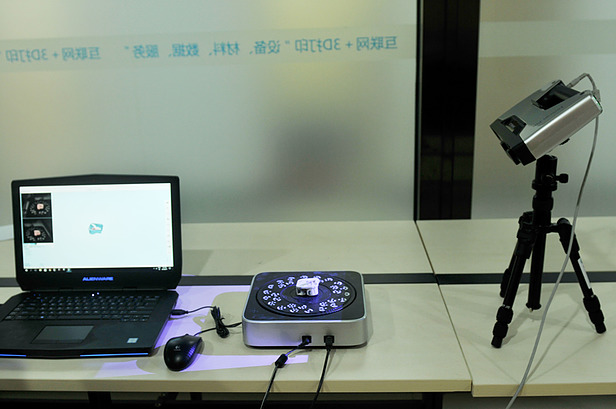
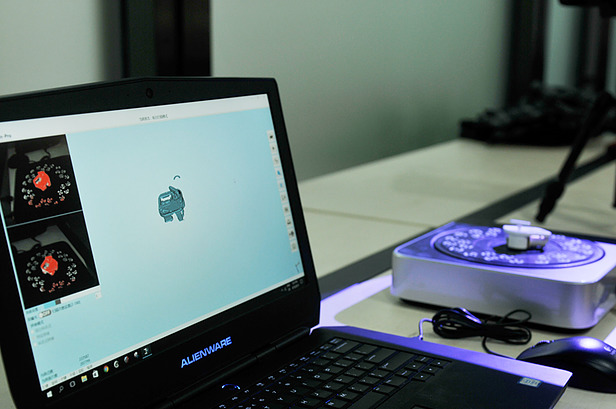
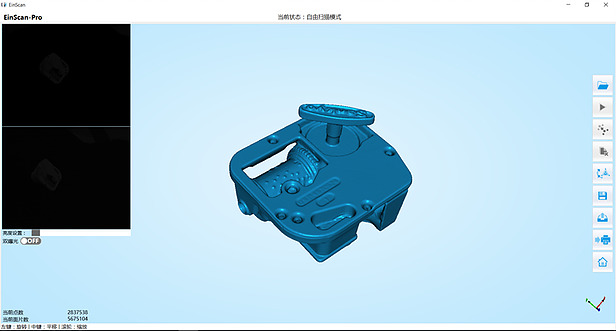
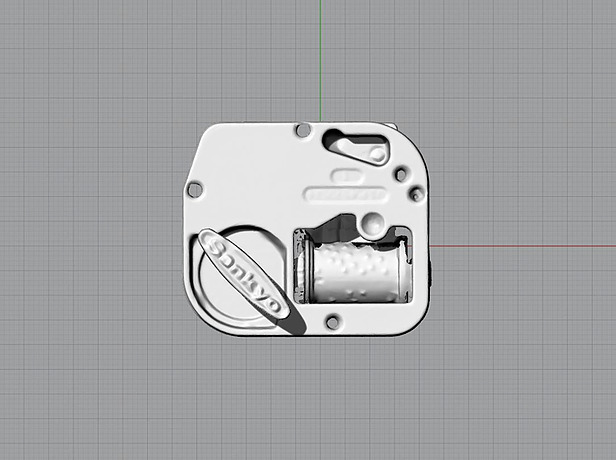
4. Assisted reverse-engineering and design
Once the designer had obtained the 3D scanned data of the European-style carved board and music box movement, the data were imported into software for reverse-engineering to aid the design of the details and structure of the artistic music box.
Designing the carved top cover of the music box:
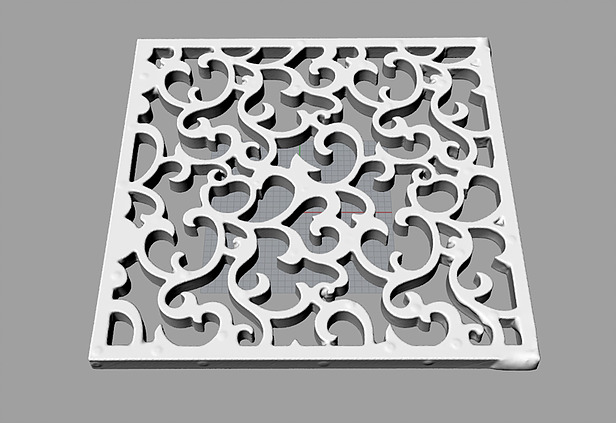
The designer imported the STL scan data of the European-style carved board into the design software. The design of the top cover of the new music box was quickly generated after amendments, extraction and copying with the scan data obtained and subsequent integration with the design model created in the early stage.
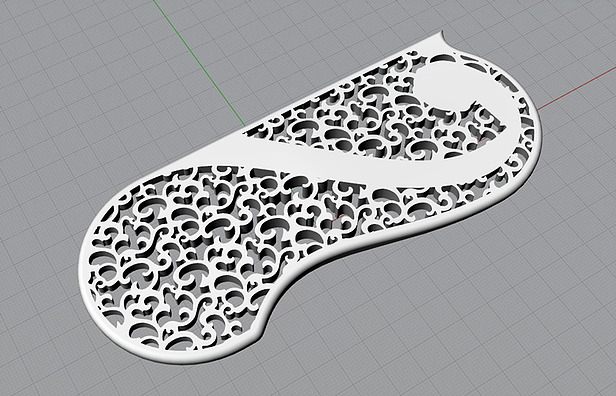
Designing the installation structure of the music box movement:
For the design of the installation structure of the music box movement, the designer imported the STL scan file into the design software. Then, he designed the structure of the music box movement to be installed into the music box using the relevant parameters from the scanned model, such as overall dimensions, screw positions and diameter, etc.
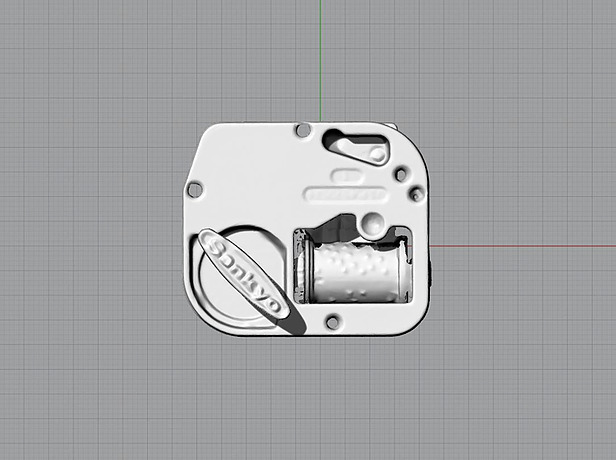
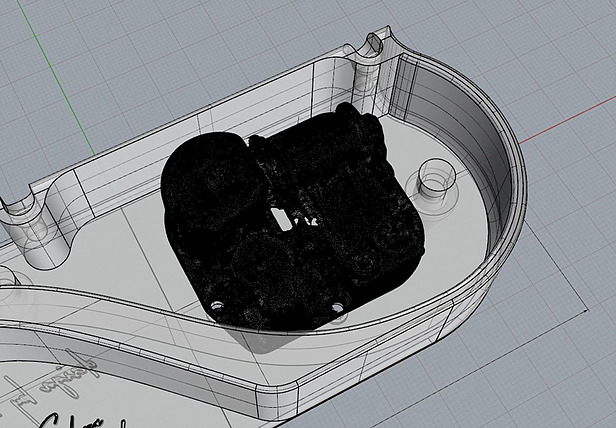
5. Printing and post-printing processing
After all the designs were completed, the designer printed out the finished product using SHINING 3D’s industrial-grade iSLA-650 3D printer. The manufacture and assembly process of the music box was completed following polishing and spray painting and with the installation of the music box movement, foot pad, and hinges.

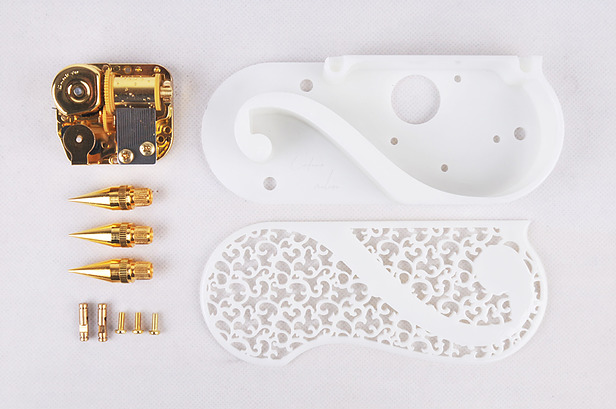
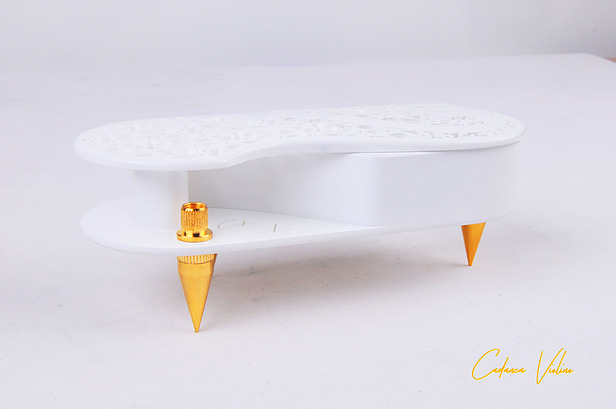
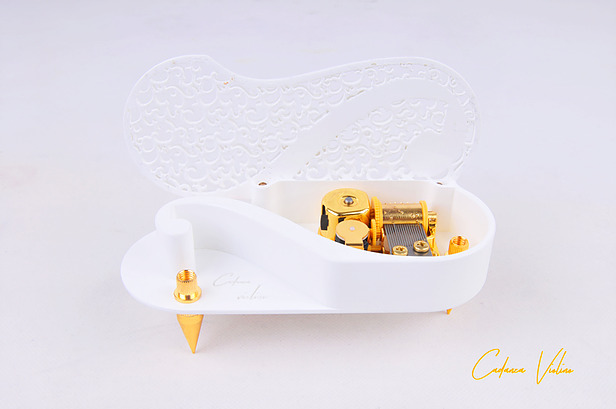
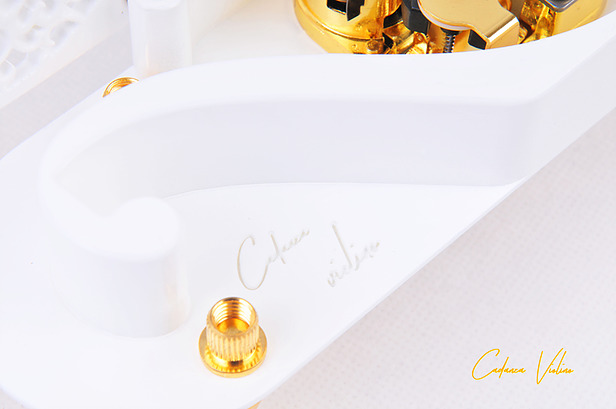