System Strobel is a commercial vehicle manufacturer specializing in ambulance, patient transport and emergency vehicles. Their main products are traditional box body constructions, converted vans and sedans, but also other specialized utility vehicles. Every vehicle, apart from motorization and power train, including furnishings is designed and manufactured in house by hand. System Strobel is exporting its products worldwide to paramedics, relief agencies, fire and police departments.
Part of the company’s DNA is relying on traditional handwork for almost every production-step. But staying true to their origins, innovation and digitalization are key factors of their evolution. So, recently the design department upgraded to an EinScan HX which they use to streamline the design and engineering process, since each vehicle is one of a kind and tailor-made for every client’s special needs.
Customizing an Audi A6 as an Emergency Vehicle
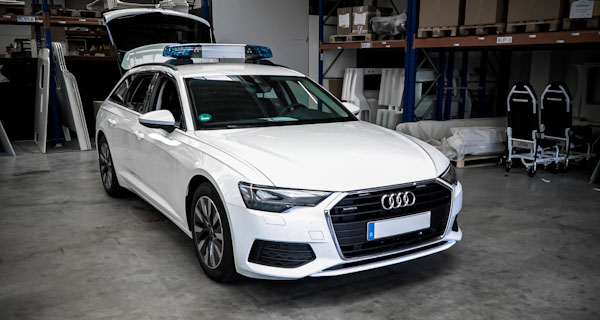
Exemplary we’ll have a look at the interior base construction of this brand-new Audi A6. This sedan once completed will serve an emergency response team, consisting of an EMT(Driver) and emergency doctor (Passenger) + additional equipment. ERT’s dispatch in conjunction with an ambulance to emergencies were an acute, life-threatening injury of a patient is present. Primarily it’s a transportation vehicle for the doctor, but it also houses a substantial amount of designated equipment, which not only needs to be stored securely but also easily accessible and functional in a highly intensive work environment. The most important part of the storage compartment is in the trunk, which contains a stainless-steel rail-based superstructure, divided into multiple heavy-duty drawers and containers.
EinScan HX: the game-changer
In the past, an engineer would take measurements of the entire trunk by hand with multiple measuring tools, to rebuild it digitally before designing the superstructure. A time-consuming, labor-intensive task prone to errors.
The EinScan HX has become a true game-changer for System Strobel as it uplevels the accuracy of measurement tremendously and reduces the time needed to collect and document all relevant characteristics of the trunk. Let´s take a look how customizing the trunk with the EinScan HX works.
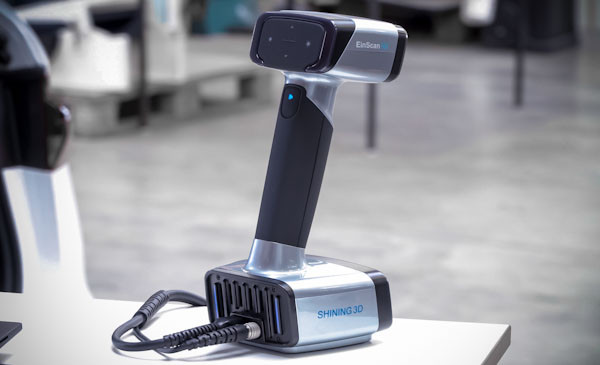
The 3D Scan Process is taking place right next to the production line. 3D Scanner and Notebook, are conveniently placed on a rolling cart. The trunk is prepared by sticking Markers on the most relevant areas. For maximum precision and because of the very dark surface, Laser Scan Mode is selected. The resolution is set to 0.05 mm. Adjustments like brightness are made on the fly while 3D scanning. 3D scanning with the EinScan HX not only eliminates the reconstruction process, but also creates a blueprint for all measuring work later on.
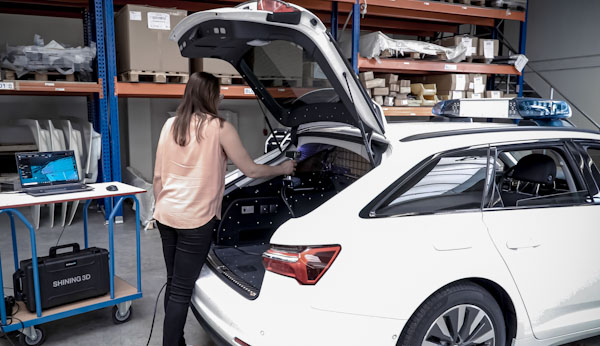
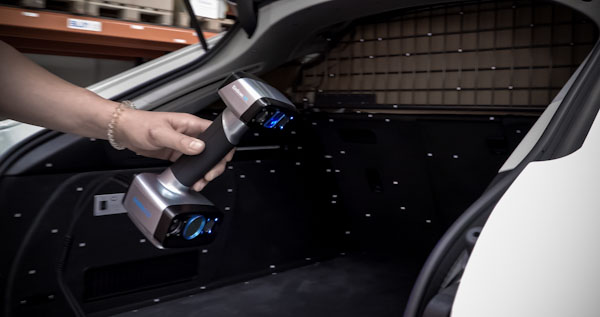
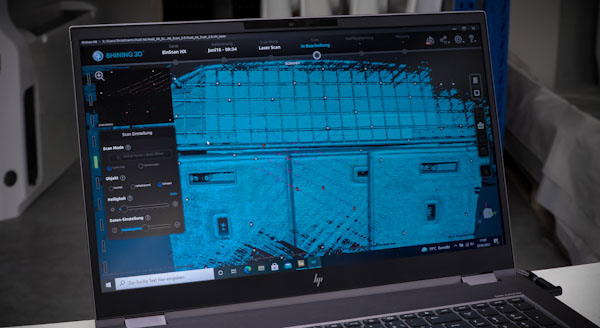
After the complete trunk has been captured in 3D, the data is evaluated and exported on site. The point cloud is post-processed with Geomagic Essentials and exported as a STEP-File, to be merged into the CAD Software.
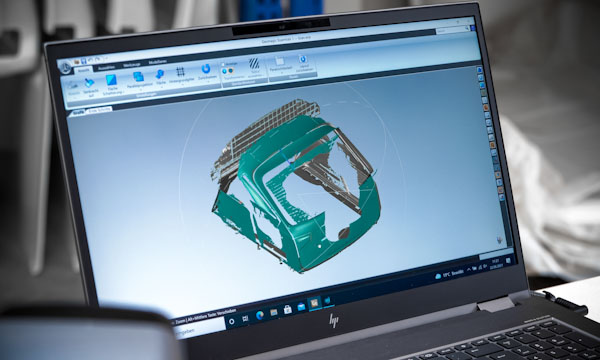
Back in the office, the 3D Design can start right away. The advantage of working with the Scan Data is that, for example, unusually shaped fasteners can be made with even greater accuracy and much less time.
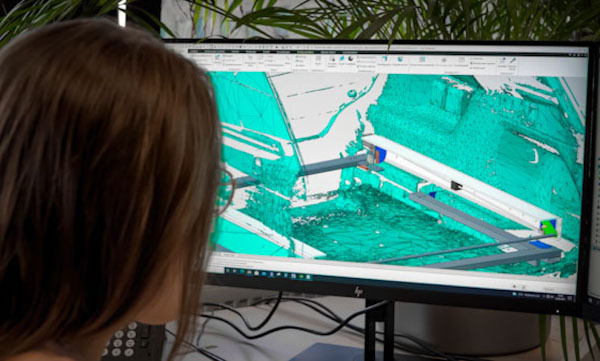
After the blueprints are completed, the components are engineered and installed in-house.
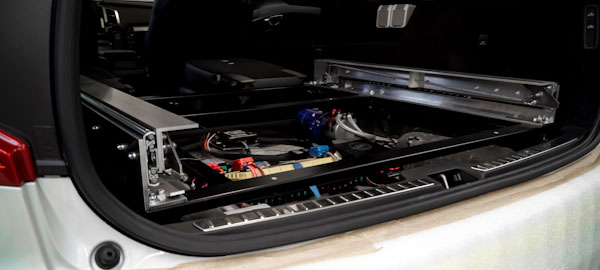
System Strobel opted for the EinScan HX due to its unrivaled flexibility and price-performance -ratio. SHINING 3D can offer fast and reliable support through its EMEA office nearby. EinScan enables System Strobel to improve and digitalize their workflow while staying true to their craftsmanship of the highest-quality, ergonomic, safe and reliable vehicles and equipment saving lives every day.