Dans le domaine de la personnalisation automobile, l’adaptation de nouveaux composants soulève souvent des défis. Cette étude de cas montre comment Sasa, un passionné de numérisation et d’impression 3D, a résolu un problème crucial de dégagement après un changement de moteur sur une Golf MK3 Cabrio. Pour cela, il a réalisé une customisation de pare-chocs avec scan 3D, de la CAO et de l’impression 3D.
- Nom : Sasa
- Localisation : Autriche
- Besoin : Installer une écope d’air sur un pare-chocs
- Solutions : EinScan Pro HD, Fusion 360, impression 3D
- Résultats : Résolution du problème du frottement du refroidisseur d’air contre le pare-chocs suite au remplacement du moteur ; la nouvelle pièce personnalisée s’adapte parfaitement et naturellement au pare-chocs.
Table of Contents
Introduction
Sasa est passionné par tout ce qui touche à la numérisation et à l’impression 3D. Travaillant dans le secteur automobile, ses compétences sont recherchées pour créer des solutions sur mesure à des défis complexes. Son parcours éducatif a été très varié. Il a fait des études supérieures dans des domaines aussi divers que l’ingénierie électrique, la mécanique automobile et l’informatique.
Il n’a pas de formation officielle dans le domaine de la numérisation et de l’impression 3D, mais grâce à l’auto-apprentissage et à la persévérance, il a pu acquérir une certaine expertise. Ce qui n’était qu’un passe-temps personnel fait désormais partie de ses projets professionnels.
Outre le projet de modification du pare-chocs dont nous parlons dans cet article, Sasa a trois autres projets passionnants en cours. Il est notamment en train de construire une voiture imprimée en 3D, de remplacer le kit de carrosserie d’une voiture électrique pour enfants et de reproduire des pièces rares sur une voiture pour enfants.
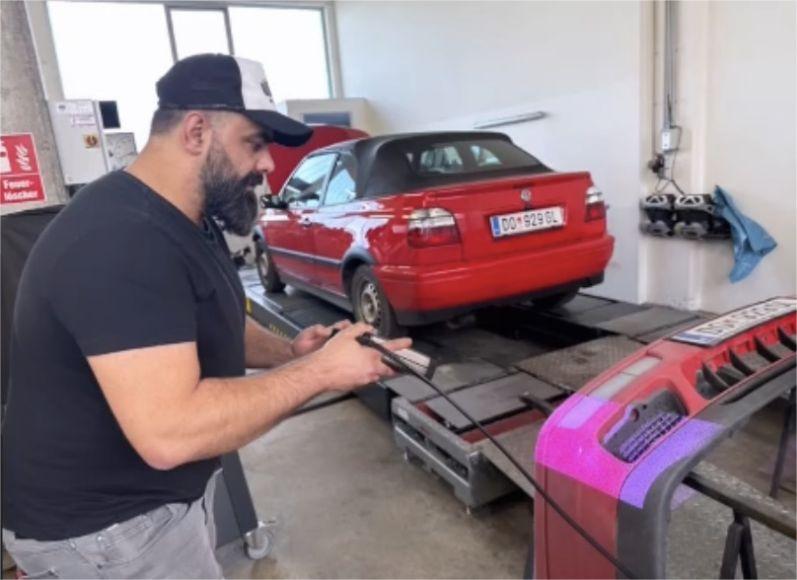
Les défis posés par le remplacement des moteurs
Le défi dans cette affaire a commencé par le remplacement d’un moteur de voiture. Le propriétaire de la voiture a installé un moteur Audi TT Turbo dans sa Golf MK3 Cabrio. Mais un problème est survenu : le refroidisseur d’air frottait contre le pare-chocs.
Le frottement du refroidisseur contre le pare-chocs peut sembler un inconvénient mineur. Mais dans le monde complexe de la personnalisation automobile, le moindre défaut d’alignement peut avoir des effets néfastes.
Lorsque ces composants entrent en contact pendant leur fonctionnement, les frottements et les vibrations peuvent entraîner une usure et des dommages au fil du temps. En outre, la tension supplémentaire exercée sur les points de fixation du pare-chocs pourrait compromettre son intégrité structurelle. Cela affecterait la sécurité globale du véhicule. Une modification était donc nécessaire pour assurer l’harmonie entre le moteur, le pare-chocs et le refroidisseur d’air d’origine.
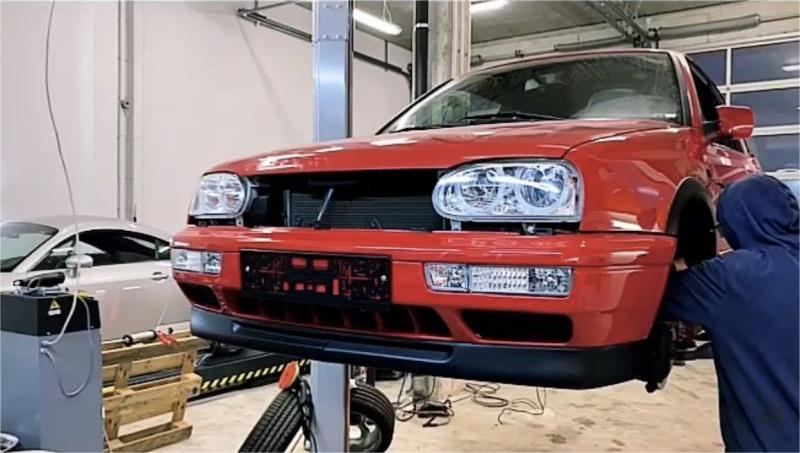
Car bumper modification with 3D scanning, CAD, and 3D printing
La solution innovante de Sasa repose sur l’utilisation du scanner 3D portable EinScan Pro HD, couplé à la CAO et à l’impression 3D. Il a décidé de construire une prise d’air aux points de contrainte afin de réduire la pression exercée sur le pare-chocs.
Sasa a d’abord vaporisé le pare-chocs avec un spray matifiant spécial numérisation 3D. Il a ensuite utilisé le mode rapide du EinScan Pro HD pour capturer le pare-chocs.
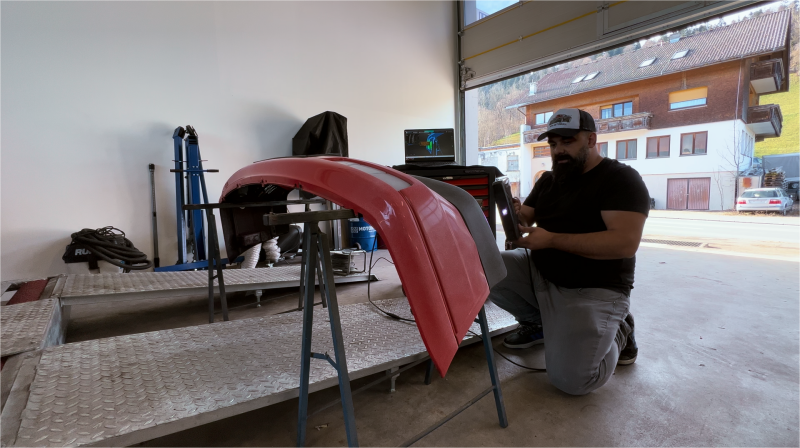
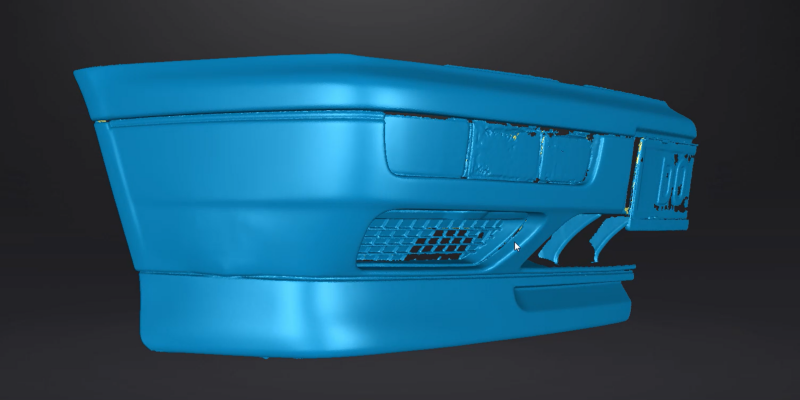
Il a ensuite affiné les données de numérisation avec Meshmixer avant de les importer dans Fusion 360.
Dans Fusion 360, Sasa a utilisé la modélisation de surface pour concevoir une écope sur mesure qui atténuerait le problème de dégagement.
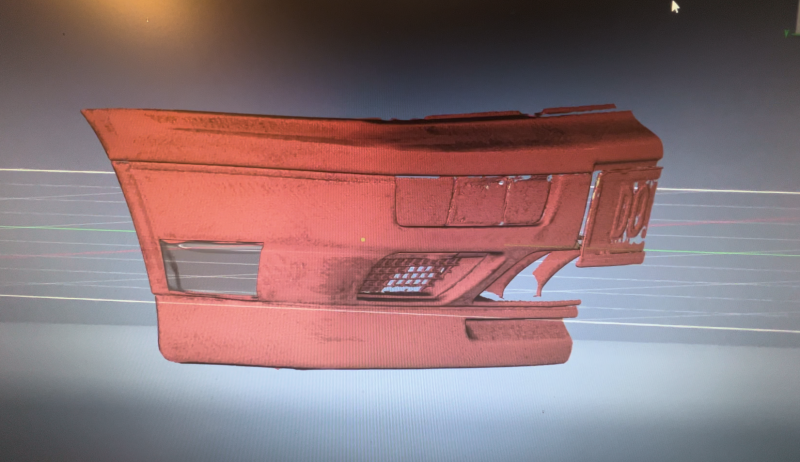
En commençant par un prototype, il a itéré sur la conception, améliorant son efficacité. Une fois l’ajustement parfait obtenu, il a imprimé l’écope en 3D et l’a intégrée à la structure du pare-chocs.
Pour assurer une finition lisse, Sasa a poncé et peint la pièce.
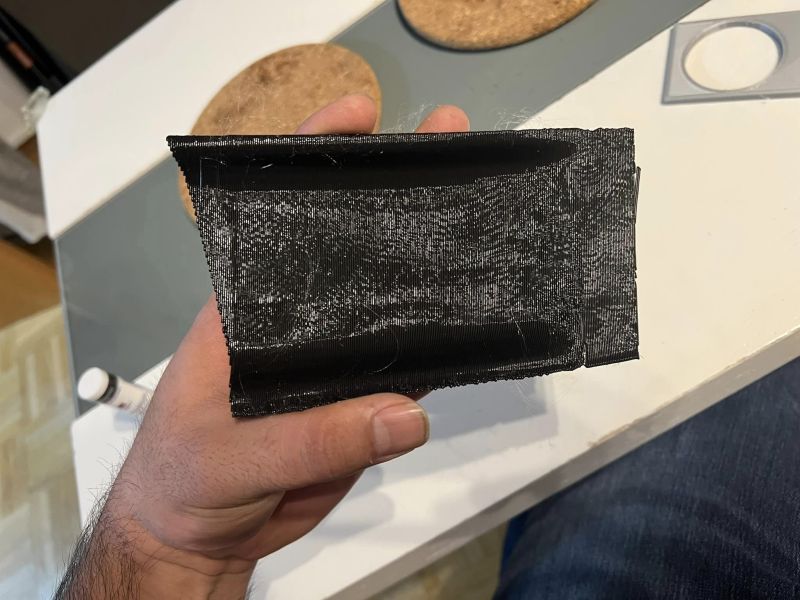
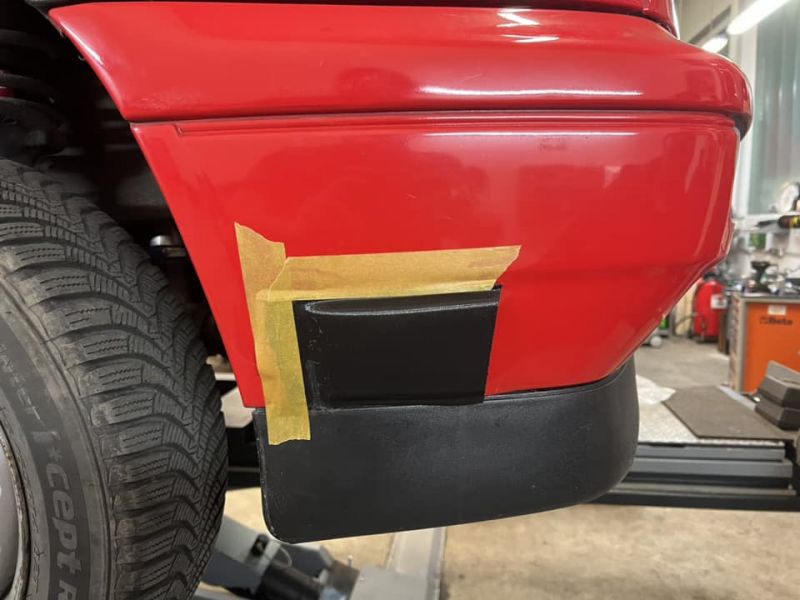
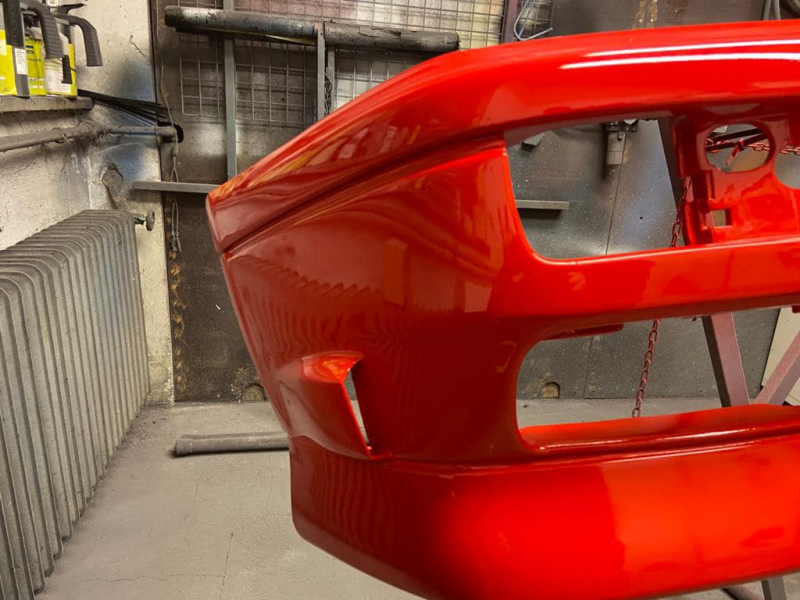
Conclusion
Sasa fait preuve d’une grande ingéniosité pour relever les défis complexes de la personnalisation automobile moderne. Sa réussite dans l’intégration de l’écope d’air, notamment grâce aux technologies de numérisation 3D, de modélisation de surface et d’impression 3D, démontre ses compétences dans ce domaine.
Cette solution lui a non seulement évité les problèmes mécaniques potentiels liés au frottement et à l’usure, mais a également préservé l’intégrité structurelle et la sécurité du véhicule.
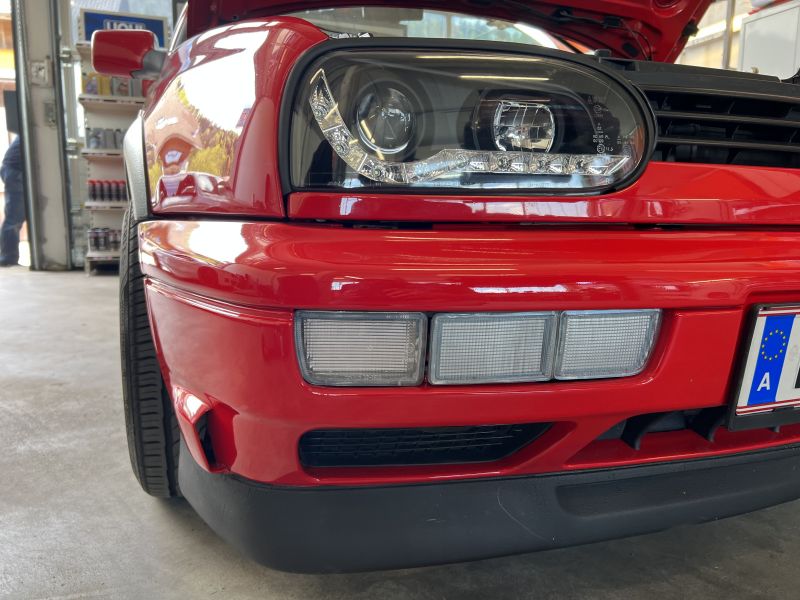
Avez-vous des difficultés à adapter des composants personnalisés dans le cadre de vos projets automobiles ? Nos solutions de pointe peuvent aider à rationaliser votre processus de conception et améliorer votre efficacité. Contactez nos experts pour une consultation gratuite et des conseils sur la façon d’utiliser les technologies 3D à votre avantage.